CPD and Polytek® Epoxy Materials
Epoxy Systems for Aerospace, Automotive, Marine, NSF Certified for Drinking Water, Pipe Repair, Sports & Recreation, and Tooling
Select a solution for your application below to learn more and view our high-performance epoxy systems that can help you achieve superb results.
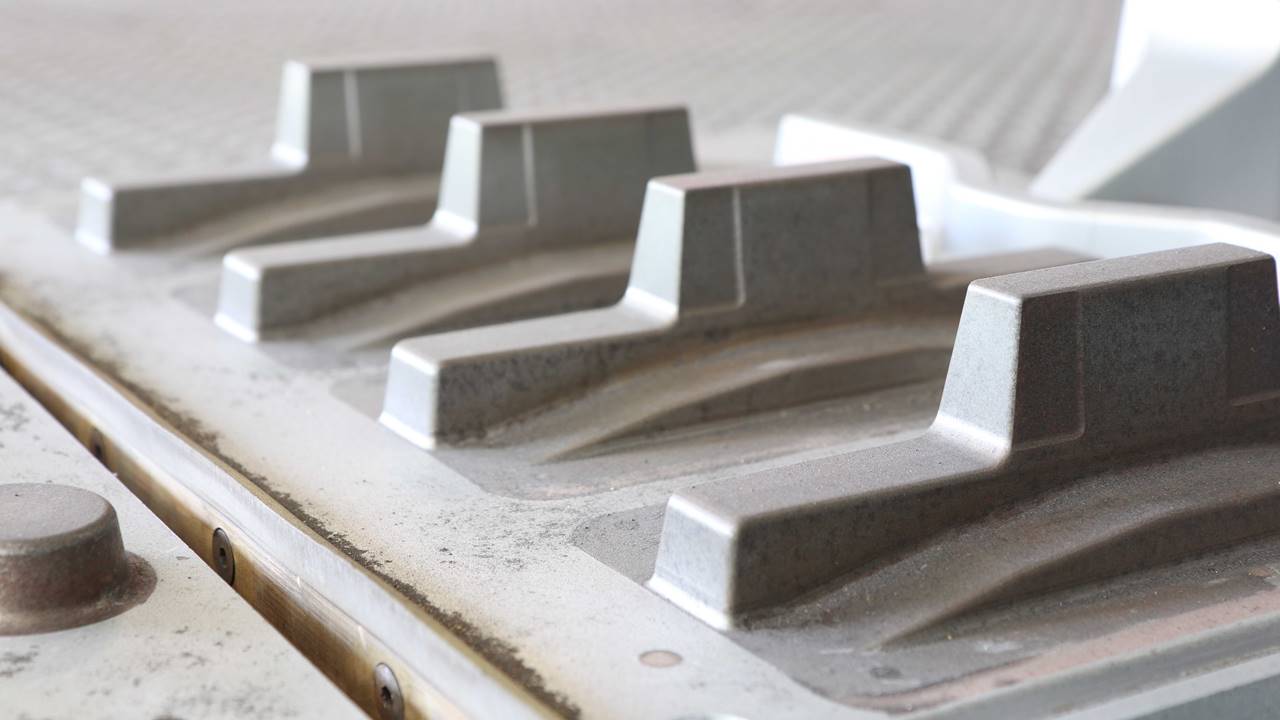
Casting Epoxies
PolyPoxy® Casting Epoxies are aluminum-filled, heat-resistant, room temperature curing (RTV) systems that are typically used for heat-resistant vacuum form tools, injection and compression molds, RTM and RIM molds, and matched dies.
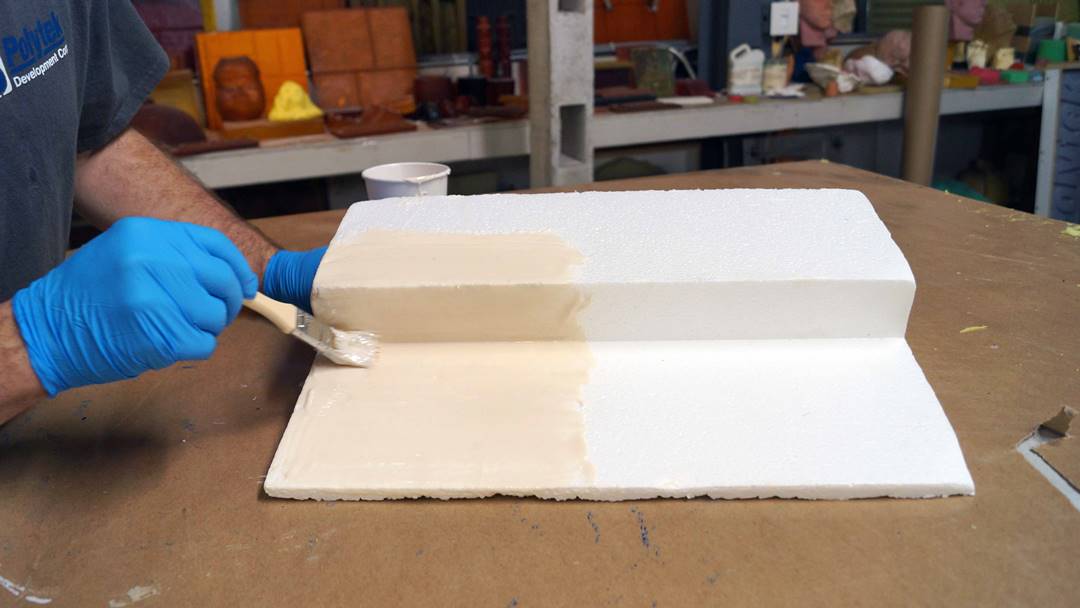
Surface Coat Epoxies
PolyPoxy® Surface Coat Epoxies are thixotropic, room temperature curing (RTV) systems for the fabrication of general purpose or heat-resistant laminated tools, including dies, foundry patterns, core boxes, and router, trim and inspection fixtures.
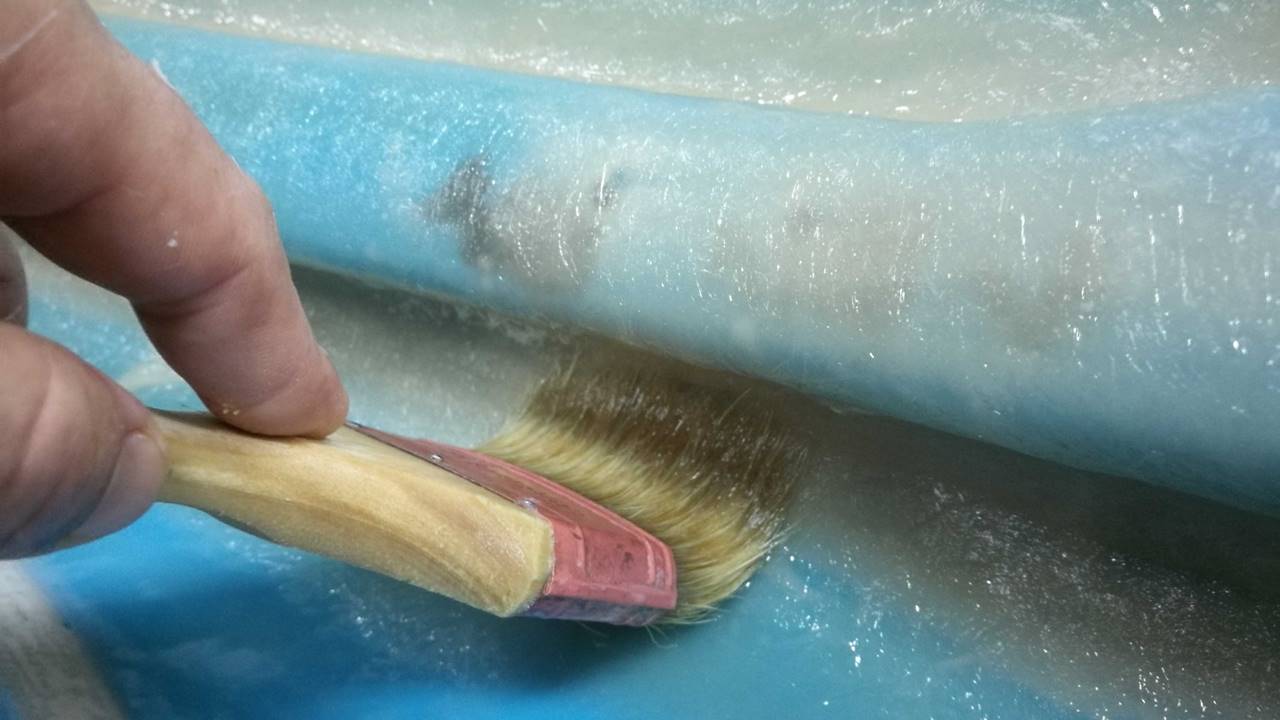
Laminating Epoxies
PolyPoxy® Laminating Epoxies are low viscosity, room temperature curing (RTV) systems formulated for general purpose and high-temperature fabrication applications.
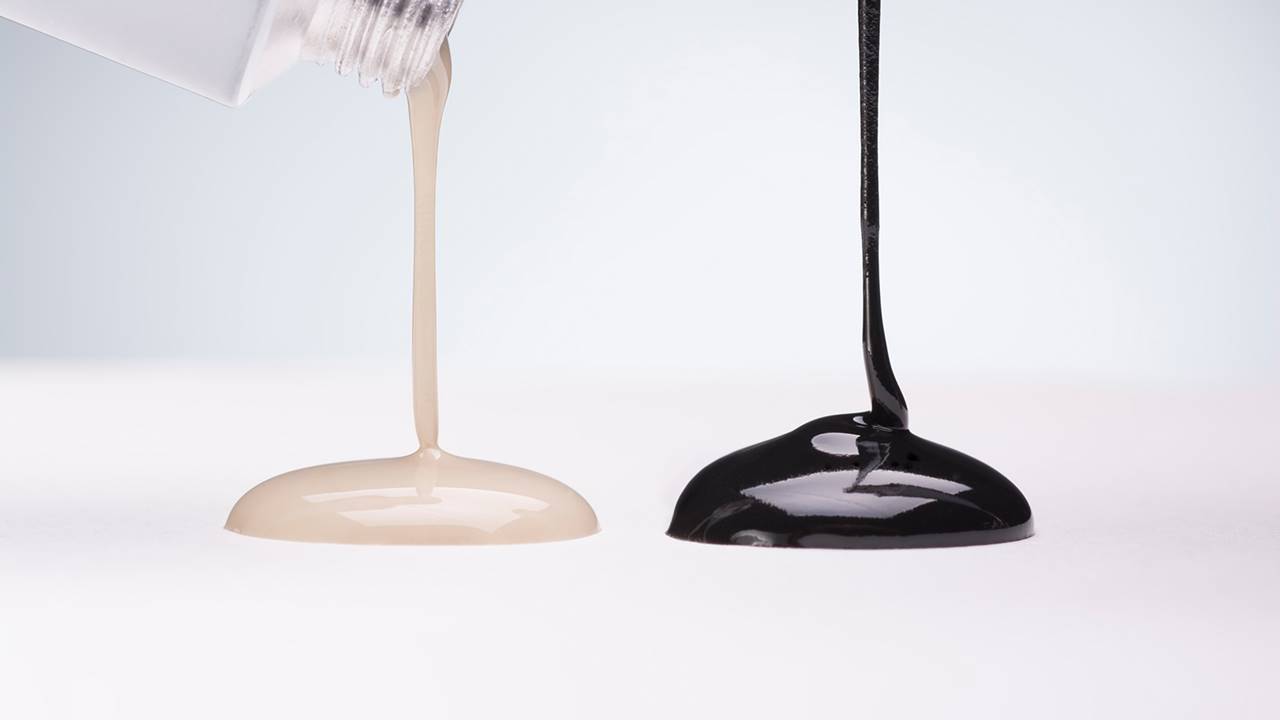
Epoxy Adhesives
PolyPoxy® Epoxy Adhesives are two-component, room-temperature curing (RTV) systems designed to be used as general-purpose adhesives as well as a bonding adhesive for TekBoard™ Tooling & Modeling Board.
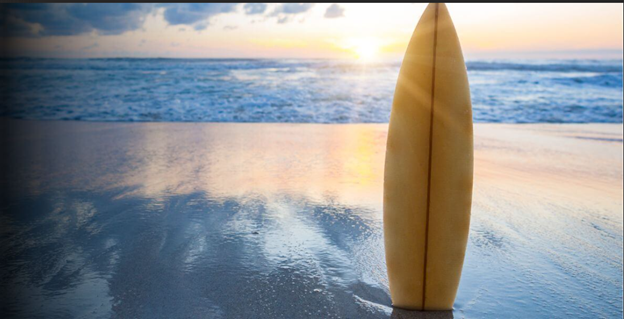
Bio-Based Epoxy Systems
CPD Bio-Based Epoxy Resin Systems are high performing resins from renewable resources that allow you to produce durable composite parts while also making a positive impact on the environment. (These systems are used for Vacuum Infusion, Resin Transfer Molding, Wet Compression Molding, and Hand Laminating Epoxy applications.)
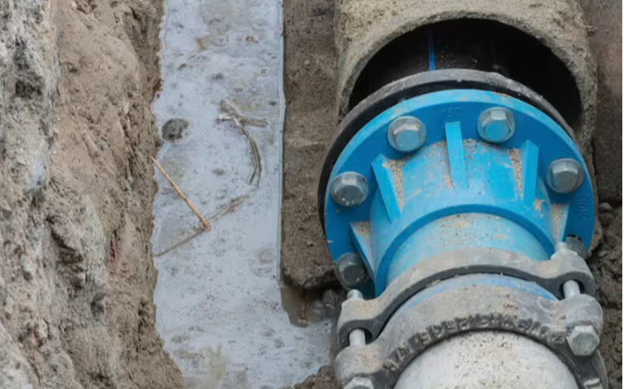
Cured in Place Pipe Epoxy Resins
CPD CIPP Epoxy resins use a single epoxy resin with multiple hardener options to allow for varied curing speeds. They are available in 4:1 and 2:1 mix ratios that are cured by hot water or steam.